De hoogste kwaliteit in combinatie met uitstekende prestaties heeft een naam: MOTOMAN
Efficient Automation: 16,500 Injection Molded Parts Packed Autonomously in 12 Hours
After completing the preliminary development and starting stable series production, the customer suddenly requested that the parts be delivered in their own packaging instead of bulk.
Given the output of around 1,400 parts per hour, this additional task was impossible to handle economically by hand. A standardized and reliable automation solution with a robot and tray stacker now performs this job efficiently.
- Industrieën
- Chemisch/kunststof
- Toepassingen
- Handling
- Klant
- EGS Automation GmbH
- Producten
- GP7 - GP-serie
Franz Wolf Kunststoffverarbeitung GmbH is a mid-sized family business in its third generation, operating for over 50 years. Located in Kirchheim, Germany, the company employs around 40 people in production, toolmaking, quality assurance, and logistics. Speaking with Petra Kaiser, managing partner, and Moritz Kaiser, technical director, they both emphasize their long-standing expertise in injection molding and their in-house toolmaking as key competencies for success. This area ensures high quality over long production runs and large quantities, while also providing the necessary flexibility for prototype development and small series.
Wolf Kunststoffverarbeitung's machinery includes around 40 machines with clamping forces ranging from 15 to 130 tons, regularly modernized. About one-third of the machines are now fully electric, positively impacting the company's energy consumption.
Customers come from sectors such as automotive, electronics, hydraulics, sensors, and communication.
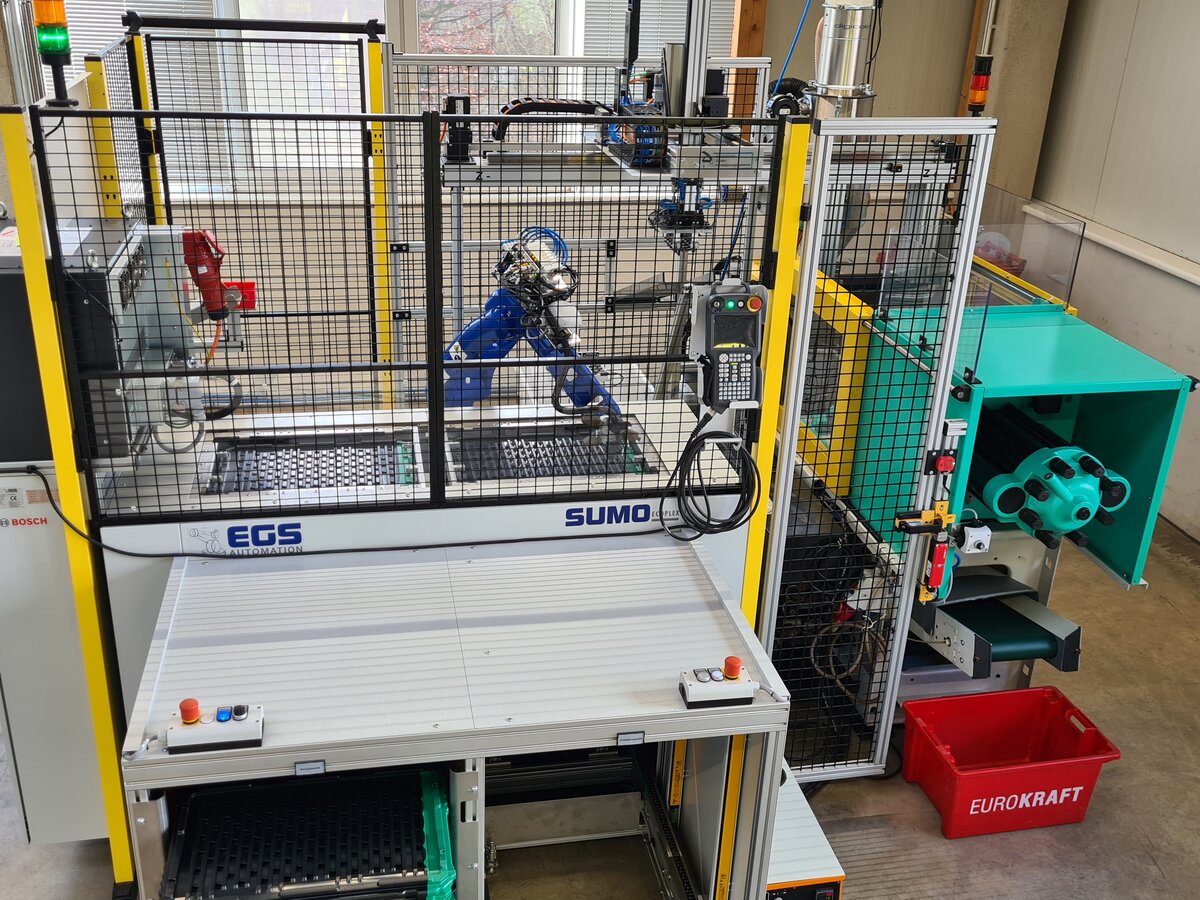
Picture: Complete system with palletizing system, robot and transfer station
One of the production lines manufactures a small precision plastic part for a steering angle sensor in large quantities. The part is molded on an Arburg Allrounder 40-ton machine with an eight-cavity mold. The entire shot is removed by a linear handling system and separated from the sprue. Each group of four parts is positioned mirror-inverted opposite the sprue. Previously, the individual parts were placed on a conveyor belt by the handling system, which then transported them unsorted into a box. The system was fully designed, built, and operational when the customer suddenly surprised Wolf with the requirement to deliver the parts individually placed in their own existing packaging.
The reason for this request is usually that the subsequent processing is automated, requiring the parts to be delivered in a way suitable for automation.
In this specific case, it meant sorting around 1,400 parts per hour correctly into customer trays measuring 600x400 millimeters, with 112 parts in each tray. The trays then needed to be stacked on Euro pallets and covered with a lid. This would have required nearly two people throughout the production time, performing a very monotonous task.
While removal handling systems are a fast and cost-effective solution for removing parts from an injection molding machine, they are not suitable for placing individual parts into trays. The existing linear handling system was therefore not a viable solution for packaging into trays. Additionally, a solution had to be found for unstacking and stacking the trays for the packaging process.
Facing this challenge, Moritz Kaiser recalled information from a newsletter sent by one of his company's customers. This long-time customer, Dunkermotoren, which receives injection molded parts from them, announced that it had acquired an automation company and now belongs to the AMETEK group.
EGS Automation from Donaueschingen has been a subsidiary of Dunkermotoren since 2021 and has been providing robot-based automation systems since 1999. Their focus is on companies in the metal and plastic processing industries. EGS offers both custom turnkey solutions and a product line of standardized automation solutions with their SUMO series.
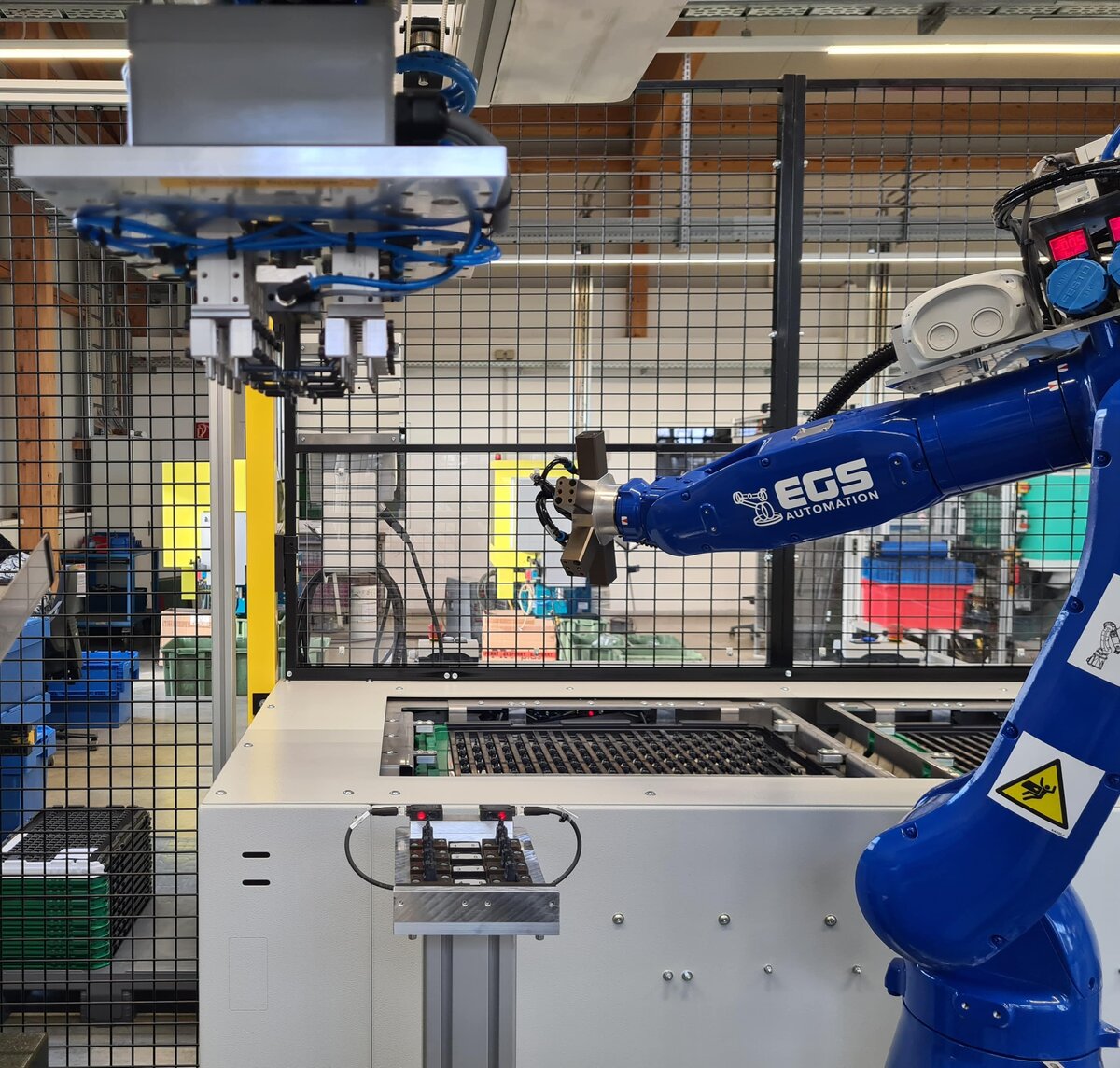
Picture: Part transfer from the removal handling system to the robot
Confronted with the task at hand, EGS was able to offer a suitable solution based on a standard palletizing system. The core of the system is the SUMO Ecoplex2, a tray stacker that can handle stacks up to 0.8 meters high in the 600x400 millimeter tray format. These can be fed and removed via conveyor belts. In this specific case, the belts hold four stacks, providing autonomy for around 12 hours.
Handling the individual parts is a Yaskawa MOTOMAN GP7 articulated robot with nearly one meter of reach and a seven-kilogram payload.
The question remained about transferring the parts from the injection molding machine. "The existing Dürrschmidt handling system should continue to handle the removal. Therefore, a transfer needed to be realized, and we were concerned about potential issues at the interface during coordination and later operation," expressed Moritz Kaiser.
Interface coordination and workspace monitoring are daily tasks for EGS. They are accustomed to adapting to different communication protocols, and in robotics, mutual space monitoring and locking individual robots against each other is standard practice. "In this specific case, Dürrschmidt's cooperative attitude made coordination very easy," noted Hartmut Pfalzgraf, responsible for this project at EGS.
Technically, the transfer was solved by having the handling system place the entire shot without the sprue into a transfer station, arranged as it is molded in the tool. Each part is monitored for presence in this station. Developed by EGS, this station is designed to be placed within the working area of both robots. Once the handling system has placed the eight parts of a shot, the Yaskawa robot rushes to the transfer station, picks up four parts one by one with a revolver gripper tool, moves to the tray ready for filling in the SUMO palletizing system, and places the four parts one by one into the next free nests. This process is repeated for the second quartet of parts from a shot. The opposite orientation of the parts from the injection mold is resolved, and each part is placed correctly. The machine molds eight parts every 21 seconds, requiring four trips between the tray and transfer station and a total of 16 pick-and-place operations, each with reorientation of the gripper tool. A challenging task that keeps the Yaskawa robot constantly moving and fully utilizing its dynamics.
Empty trays enter the tray stacker in a stack and are lifted and presented to the robot for filling. Once a tray is filled, it is placed on the stack of full trays until the stack reaches its full height and is conveyed out. The conveyor systems at the entry and exit of the palletizing system each hold space for four stacks of empty and four stacks of filled trays. The system can run autonomously for around 12 hours. "An operator only needs to transfer four filled stacks from the conveyor to a Euro pallet every 12 hours, move the pallet away, bring a new empty Euro pallet, and set up four new stacks of empty trays. All in all, less than ten minutes of work, and then the automation runs autonomously for another 12 hours," Moritz Kaiser happily explains
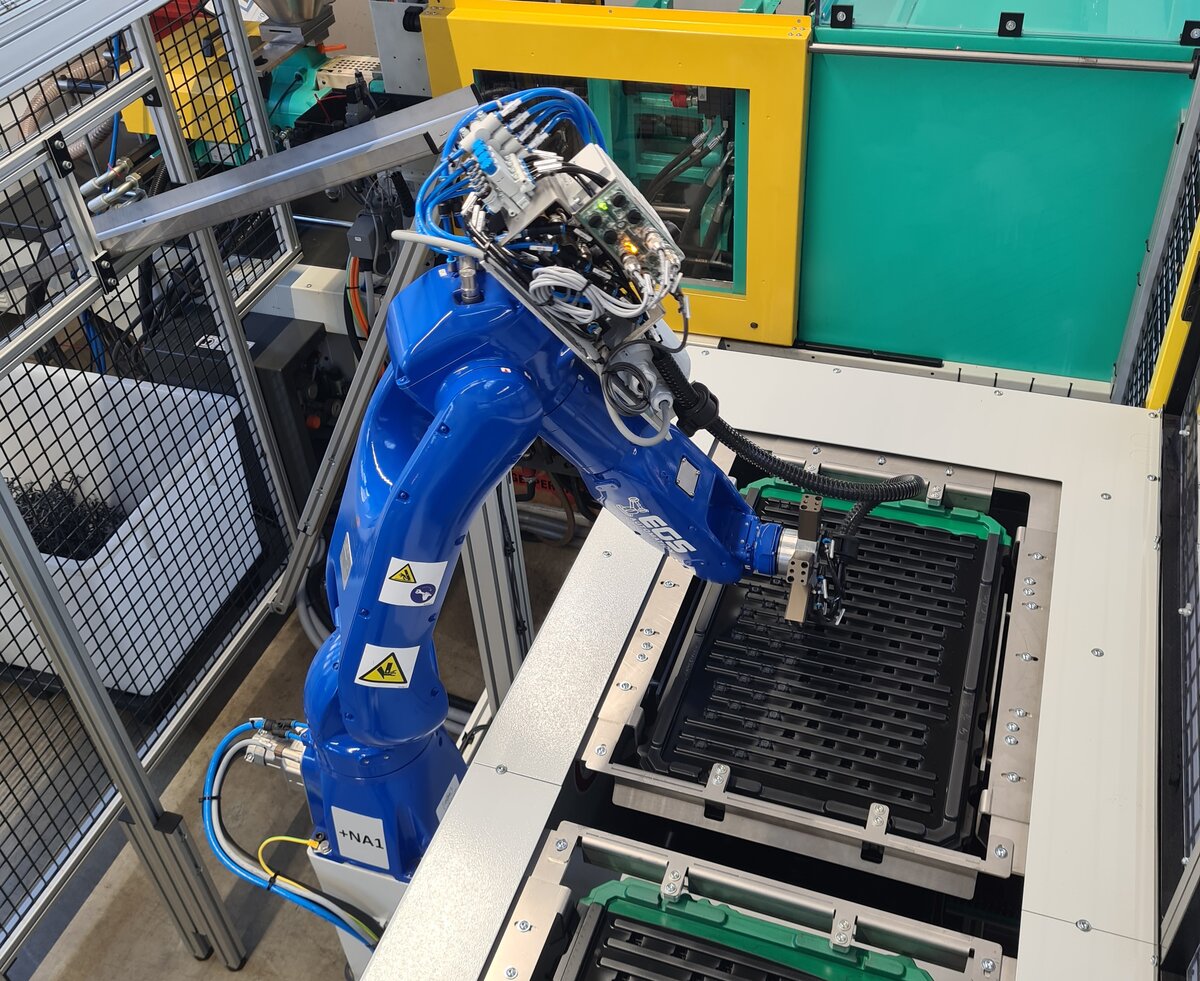
Picture: The robot places eight finished parts in the nests of the trays in 21 seconds
With this system, the first articulated robot has been introduced into the production of Franz Wolf Kunststoffverarbeitung. Initial fears and reservations proved unfounded. The installation and handover of the system included a two-day training session for the operating personnel on how to use the system and handle potential breakdowns and issues. The robot programming handheld device is not required for operating the system. If assistance from EGS is needed, it can be quickly provided remotely via the integrated remote maintenance module. "Robot programming skills are not necessary for operating the system. However, we have taken a liking to robotics with its flexibility and reliability. This won't be the last robot in our production, and we want to gradually delve deeper into the topic. EGS supports us exactly as we want and need," praises Petra Kaiser, looking forward to the near future.
"We were also very surprised by the detailed and illustrative system documentation and user manual that came with the system. It's clearly not just documentation to comply with standards and regulations but also made to be practical for regular use," concludes Moritz Kaiser.
The automation was integrated into the existing spatial conditions without needing to move the machine and aggregates. The SUMO system allows for largely free alignment of the palletizing system to the robot, so the operator side can be optimally aligned with material logistics.
Author: Heiko Röhrig; Senior Business Development Manager at EGS Automation
Pictures: ©EGS Automation